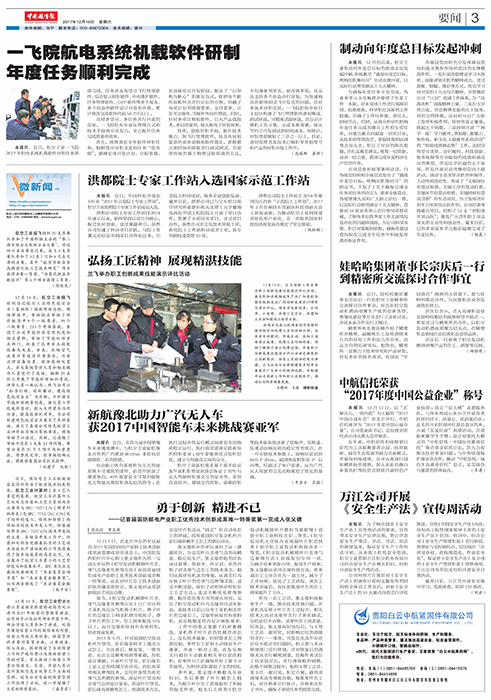
勇于创新 精进不已
——记首届国防邮电产业职工优秀技术创新成果唯一特等奖第一完成人张义德
通讯员 罗志英
12月7日,在北京举办的军民融合2017年国防邮电产业职工技术创新成果展览暨成果洽谈会上,中国航发西航叶片中心职工张义德作为第一完成人申报的《航空发动机精锻叶片进、排气边缘柔性磨削方法》获得首届国防邮电产业职工优秀技术创新成果唯一特等奖。这是对叶片加工技术创新团队的褒奖和肯定。张义德对这项创新做出了突出贡献。
如今,《航空发动机精锻叶片进、排气边缘柔性磨削方法》已广泛应用于某机高压压气机转子叶片、静子叶片的边缘加工和某机增压级转子、静子叶片的加工中,加工效率提高15%以上,而且边缘形状得到有效控制,经济效益显著。
2011年5月,针对我国航空发动机叶片型面、前后缘采用手工抛光方式加工,方法落后、精度低、一致性差、无法实现精密检测等难题,西航设立课题,开展叶片型面、前后缘加工新工艺和检测方法研究。西航拟采用相关磨削技术,实现叶身型面和进排气边的数控磨削,满足叶片型面和进排气边的设计要求,形成叶片型面、前后缘高效精密加工、检测技术方法,实现叶片制造从“技艺”到自动化加工的跨越,扭转我国航空发动机叶片前后缘依赖手工加工的落后局面。
张义德所在的单位承担了这一课题项目。为实现叶片进排气边的高精度、稳定化生产,张义德和他的团队成员赵赟、张新冬、许立君、余杰开始了对进排气边加工的技术攻关。他们认真研究机床的性能,认真进行高压转子叶片的进排气边磨削试验。通过不断试验,得到了对称路径控制加工工艺方法;通过不断优化磨削参数、程序优化等方面的深入研究,实现了航空发动机叶片边缘的自动化制造,该技术目前已应用于某机相关叶片的边缘加工,边缘形状得到有效控制,表面粗糙度符合设计图纸要求。
工作中的张义德敢于向困难挑战。某机静子叶片在西航属首次加工,没有技术储备,同时要求加工周期很短。零件加工前他主动做好生产准备,并逐一核对工装。在发现相关问题后主动联系相关单位更改抢制,在零件开工前确保所有工装可正常使用,为科研试制赢得了宝贵时间。
多年来,张义德不断提高专业知识,先后掌握了叶片精加工技术,为提升叶片加工质量起到了积极的促进作用。他先后主持的《航空发动机精锻叶片数控当量磨削》曾获中航工业科技进步二等奖,《航空发动机大型钛合金风扇叶片制造技术》获中航工业发动机科技进步一等奖,《航空发动机精锻叶片进排气边磨削方法》获得发明专利一项。
为减少设备资源占用、提高生产效率,张义德提出采用合理有效方法,将多道加工工序合并为一道工序,减少了工序周转,优化了工艺流程,该加工技术突破后,高压圆弧齿叶片的加工效率提升了15%。
作为一名工艺员,张义德积极服务生产一线,解决技术质量问题。在某机高压转子叶片加工过程中,相关技术人员对该零件进行了多次调试,但结论仍不合格。该零件加工周期紧、任务急,张义德得知情况后,与主管工艺员一起研究,对影响定位的测量销进行一一排查,当发现夹具中存在定位不稳定的问题时,他立即与夹具修理部门进行修理,并对修复后的浇铸夹具进行精密测量,经操作者试加工结论稳定后,进行浇铸模的调整。在整个调整过程中,他和主管工艺员、室主任一起讨论,制定方案,最终该浇铸夹具先锋批合格,整批零件加工后,对合格率进行统计,合格率达到了99%,确保了该项任务的按期完成。