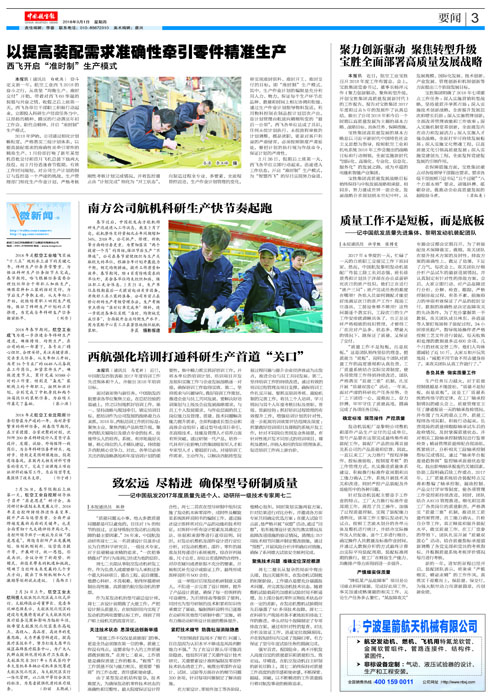
质量工作不是短板,而是底板
——记中国航发质量先进集体、黎明发动机装配团队
本报通讯员 杜学胜 张博雯
2017年4季度的一天,忙碌了一天的白班职工交接完工作下班回家,然而,中国航发黎明发动机装配厂传装工段工长刘志强、班长徐景秀和计划员于洋却在办公桌前研究次日的班产组织。他们正在进行“班产三问”:班产完成任务的难度在哪里?各组人员如何调配才能更好地满足次日的班产工作?现场工位器具、工装设备够不够用?这些问题逐个落实后,工段次日的生产工作安排就清晰具体了。也正是这样严格细致的组织管理,才使得工厂在应对产品多、状态多、增量大的情况下,既保证了质量,又保证了交付。
“质量工作不是短板,而是底板。”这是团队始终坚信的理念。把质量当“底板”,说明这个团队对质量工作的高度重视和认真负责。工厂质量系统结合实际完善制度,使各项管理工作得到持续改进。团队严格落实“质量三谁”机制,扎实开展“质量双放心”活动。一年来,面对严峻的科研批产任务形势,全厂上下团结一心,迎难而上,奋力拼搏,牢牢守住了质量高地,圆满完成了各项任务目标,
确定标准 规范操作 严控质量
发动机装配厂是黎明公司整机和部件产品生产交付的总成单位,型号产品要在这里完成最终集件和装配工作。装配厂产品的良莠直接关系公司的产品质量和信誉。因此,一直以来工厂大力推行“按程序操作、按标准验收、按制度考核”的工作管理方式,扎实推进质量体系建设,积极推行标准作业周期和员工能力确认工作,系统开展技术攻关和改进,同时严控产品装配及外场使用中的各种问题。
针对发动机装配主要是手工作业的特点,工厂大力推行标准作业周期工作,规范了员工操作、加强了过程质量控制、实现了装配能力透明化。该项工作主要以发动机为试点,按照工艺流水划分的各单元体及整机进行统计,并结合实际操作及人员配备,逐个工步进行细分,确定操作人员数量及标准作业时间,并通过大数据分析的方式最终计算出实际平均装配周期。装配标准周期的推行,使工厂在释放生产能力、均衡排产等方面得到进一步提升。
严慎细实保质量
“降低某产品故障率”项目是公司重点科研课题。完成好此项工作,事关加速成熟课题的相关工作。无论生产任务多么繁忙,“某故障攻关”专题会议都会定期召开。为了将装配技术保障做实、做细,攻关团队在提升技术方案的及时性、排故方案的准确性上,做足了功课,下足了力气。每次会上,攻关团队仔细分析产品试车的最新进展情况,并认真制定有针对性的排故方案。会后,大家立即行动,对产品故障进行分析、分解、检查、跟踪,严格控制排故过程。有条不紊、措施得力的举措有效保证了产品的按时交付。数据的准确性是决定故障攻关的先决条件,为了充分掌握第一手数据,攻关团队成员林东、孙逍遥等人紧盯现场转子装配过程,24小时排班跟产,指导现场操作者严格按照工艺文件进行装配,每天收集和处理的数据量多达600余项。几个月的昼夜交替工作,他们人均体重减轻了近10斤,大家互相开玩笑地说:“减肥不用节食不用去健身房了,来攻关团队认真工作就行了。”
各负其责 做实质量工作
生产任务压力越大,对于质量控制就越是不能放松。“质量不是短板,而是底板”,这是工厂质量系统始终恪守的定律。在工厂轴承控制情况的碰头会上,质量管理室主任丁静通报前一天的轴承故检情况,并布置了当天的重点工作。质量工程师各司其职,积极行动起来。负责现场的质量师跟踪轴承试车后的故检情况,及时掌握质量状态,并对相关工段轴承控制情况进行监督检查;精益管理质量师配合现场组,抓紧统计、分析相关工段轴承控制指标完成情况,通过“轴承单台报废量趋势图”监控轴承质量状态变化,找出影响轴承报废的关键因素,协助工段明确后续工作重点。2017年,工厂质量系统结合装配特点完善和整编了轴承控制、漏油控制、产品交付评审等制度,使各项管理工作受控和持续改进。同时,团队结合AEOS管理推进,细化和完善工厂各类岗位的质量职责,严格落实“质量三谁”机制,推进员工质量档案管理、员工能力确认、自检自分等工作,真正释放和提升装配水平,做实质量工作。在工厂党委的带领下,团队扎实开展“质量双放心”活动,结合质量指标承接重新调整了各党支部和党员的考核指标,并根据质量系统考核评价情况每月进行考核。
新的一年,进军的征程已经开启,装配团队表示,将秉承“严慎细实、精益求精”的工作作风,真抓实干迎难而上,保质量、保交付,为强大航空动力再谱新篇章,再创新业绩。