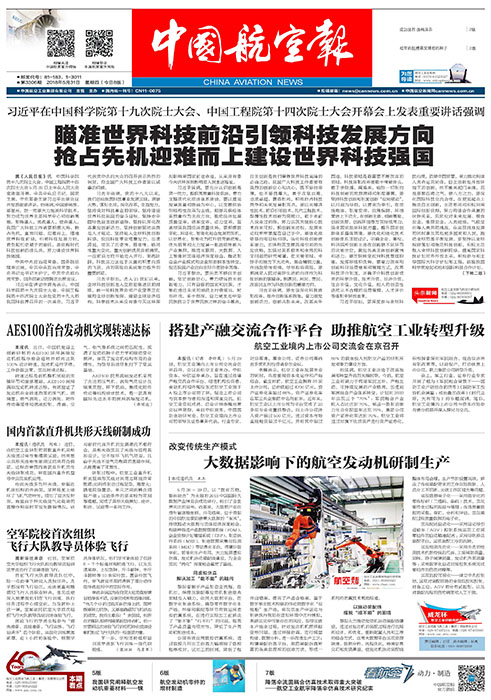
改变传统生产模式
大数据影响下的航空发动机研制生产
王玉 摄
本报通讯员 王玉
5月26~29日,以“数化万物,智在融合”为主题的2018中国国际大数据产业博览会成功举行,吸引了全世界关注的目光。近年来,大数据产业在贵州省落地生根、开花结果。位于贵阳的中国航发黎阳借着大数据的“东风”,持续推动大数据与实体经济深度融合,构建并畅通产品数据管理系统(PDM)、企业资源计划管理系统(ERP)、制造执行系统(MES)、制造数据采集与监测系统(MDC)等信息化平台,搭建好数字化、智能化生产布局,大力发展虚拟仿真、发动机脉动装配线建设,为企业实现“两化”深度融合奠定了基础。
用虚拟仿真解决加工“能不能”的疑问
黎阳着眼于产品制造全流程,在机加、焊接及装配等发动机制造重点领域投入精力,依托大数据平台,在数字化制造系统、典型零件数字化生产线、焊接和装配等环节有效运用虚拟仿真系统,在进行实际加工前解决了“能不能”“行不行”的问题,提高了产品质量与稳定性,降低了生产周期和制造成本。
公司有效应用数控仿真系统,通过数控几何加工仿真大幅缩短了数控程序校对、试加工的时间,降低了程序出错率,提高了产品合格率。基于数字孪生技术构建的作动筒数字化“双胞胎”生产线,将现实生产中活动与制造执行规划在虚拟环境中进行模拟,规避现实中可能存在的风险,指导实体生产线全过程。针对发动机机匣焊接变形问题,通过焊接仿真,进行模型构建、数据分析,进一步改进生产工艺;构建装配仿真平台、规范装配仿真所需的各类资源库的创建方法,形成一系列的仿真技术规范标准。
以脉动装配线摆脱“顺不顺”的困境
黎阳大力推动发动机脉动装配线建设,通过对发动机的装配过程进行流程再设计、再优化,重新配置人员和工序的组合方式,应用大数据平台实现资源融通、数据分析、流程优化,畅通信息交汇和反馈渠道,使发动机脉动装配线整体布局合理,生产节拍设置高效,解决了传统装配带来的工作现场拥挤、人员分工不明晰、无效工作区域大等问题。
实现数据电子化——采用数字化的零件标识(二维码、条码)技术,实现零件全过程的跟踪与管理;在线质量数据的采集、存贮、分析和评估,实现装配过程质量数据的电子化。
实现配送自动化——采用自动导引运输车(AGV)控制系统实现工位间零组件的自动精准配送;采用导轨移动装配平台,实现装配工序的流转。
实现检测先进化——采用先进的检测技术代替传统的尺表、工装辅助测量,如转、静子间隙测量、发动机外廓测量等;采用数字化自动对接控制系统完成零组件的自动对接等。
实现监控可视化——建立中央控制站,实现对装配现场的全面监控和控制,对各工位、AGV的分布式控制,以及对装配流程的自动调度和人工干预。