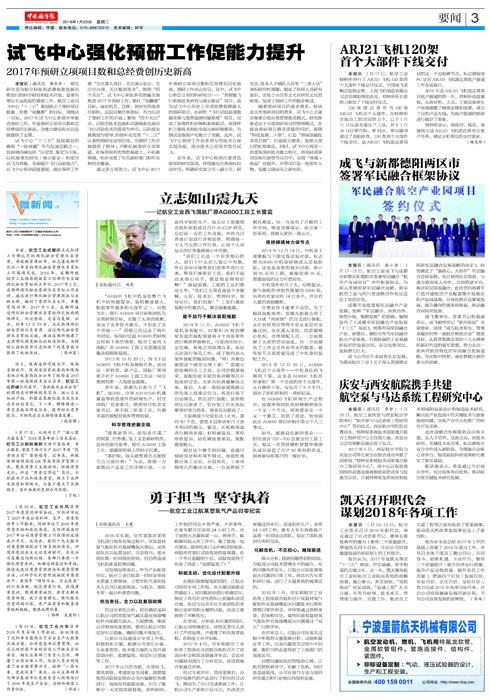
立志如山震九天
——记航空工业西飞国航厂原AG600工段工长雷震

本报通讯员 周莉
“AG600飞机中机身是整个飞机中结构最复杂、装机难度最大、配套零件最多的大部件之一。回想当年,我们AG600项目研制团队为实现研制目标,克服了太多的困难,攻克了太多技术难关,才创造了这个奇迹……”即使已经过去了两年半时间,每每回忆起AG600的研制过程和下架的情景,航空工业西飞国航厂原AG600工段工长雷震还是激动得眼眶湿润。
2013年10月29日,西飞下达AG600飞机中机身装配任务。面对这一新机型、新产品,国航厂领导班子对于AG600工段工长这一岗位想到的第一人选就是雷震。
多年来,雷震先后参与了“飞豹”、MD90、空客A319/320机翼翼盒等机型部件的研制生产,时任国航厂党委委员、欧洲项目组党支部书记、英宇航三阶段工长,有着丰富的装配经验和管理经验。
科学管理把握全局
“既做新型号,就知责任重。”时间紧、任务重,加上又是新研机型,没有经验可参考。接任AG600工段工长,雷震深知肩上的担子沉重。
“那时候,每天就想着怎么能按节点完成任务!”为此,雷震一方面做出产品加工的详细计划,一方面科学组织生产。每天早上雷震都会组织班组成员召开SQCDP例会,总结前一天的工作进展,并将当日各类计划进行详细安排,明确每一个人当天的工作任务,让每个人对每天的任务量做到心中有数。
“我们工长是一个非常细心的人,我们干什么活儿他心中有数,所以会早早地帮我们把零件进行分类,帮我们准备好工具。我们干起活来得心应手,都是他安排得好啊!”提起雷震,工段的工友们都这么夸。“我们工长简直就是个全能啊,人好、技术好、管理科学,领导信任,我们也服!”工友们遇到装配中的难活儿,都会请教雷震。
能干加巧干解决装配难题
2014年11月,AG600飞机下部机身装配中,33框和35框的横梁角盒的装配需要将4个角形零件进行精准拼接制孔,可是因空间小、定位难、各角之间协调点多,风钻无法进行制孔工作,成了制约该大部件装配的瓶颈问题。“啃!再难也要把这个硬骨头啃下来!”雷震立即协调相关工艺员、公司劳模郝海荣、装配经验丰富的朱昔峰等召开现场研讨会,大家共同商量解决方案。最后,大家一致同意雷震提出的先架上找准定位点,再进行架下台钻制孔,然后进行装配。虽然程序比以前多了,但台钻工作比风钻要省时省力得多,效率反而提高了。
主起落架下位锁长达1.8米,重约40千克,要把4层形状和尺寸各不相同的接头、蒙皮、长桁和角盒进行精准连接,材料硬度高、零件形状复杂、钻孔精度要求高,装配难度极大。
面对这个棘手的问题,雷震仔细研究材料和零件特点,创造性地提出架上定位,分层制孔,上架再制终孔的解决方案,一方面降低了制孔难度,另一方面有了开敞的工作空间,精度也能保证。该方案一经采用,得到大家的一致认可。
用拼搏精神力保节点
2014年12月14日,中机身上部壁板与下部实现总装对接,标志着AG600中机身研制进入总装阶段,这也是攻坚的最后时刻。原计划25天的工期,被缩短到15天,雷震面临的压力可想而知。
中机身外形尺寸大,结构复杂,参与装配的零组件数量约3200项,另外约有紧固件14万多个,并且有大量的高锁螺栓。
合理安排才能事半功倍。为了提高装配效率,雷震大胆提出将工人分成“两班倒”的方式进行装配。这在新研项目管理中是从来没有实施过的,存在重大风险。但雷震精心组织,合理调配人员,一方面缓解了大家的劳动强度,另一方面避免了工序交叉作业带来的隐患,最终按节点高质量完成了中机身的装配工作。
2014年12月29日,AG600飞机首个大部件——中机身在西飞顺利下架,这也是AG600飞机所有承制厂第一个完成的首个大部件。从开铆到下架,仅仅用了8个半月,创出了新机研制的一项新纪录。
在AG600飞机研制生产过程中,雷震率领团队用拼搏精神保住一个又一个节点,用智慧攻克一个又一个难关,创造了奇迹。他也因此在AG600项目研制中荣立个人三等功。
如今,雷震肩负新的使命——担任波音737-700总装交付工段工长,他又一次用拼搏和智慧率领团队成员创造了月产30架份的奇迹,得到领导和客户的一致好评。