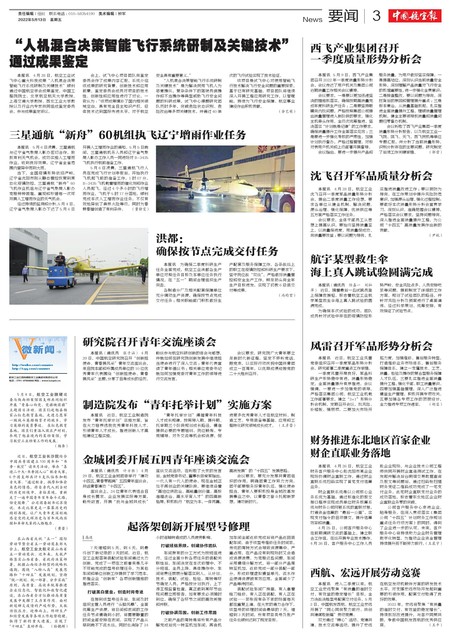
起落架创新开展型号修理
高进
7天缩短到5天、到4天,到最终创下新纪录的3天时间。近日,航空工业起落架装配试验车间通过大力创新,完成了一项在之前看来是几乎不可能完成的型号修理任务,为其他车间和单位创新工作提供了学习范本,助推企业“创新年”各项创新措施的推进落实。
打破黑白壁垒,创造时间奇迹
在接到该型号任务后,车间及时组织主管人员进行“头脑风暴”,全面统筹生产资源,将日间和夜间的工作任务节点精确到小时,将需要静置的时间全部安排在夜间,实现了产品从早到晚不下流水线,同时也消除了24小时连轴转造成的人员疲劳影响。
打破班组界限,创建协作团队
车间原有的分工方式为按班组进行。经过全面分析各项任务的装配关联性后,车间决定在本次修理中,不分班组,全员上阵。具体操作中,车间将责任层层分解落实到人,从计划、技术、装配、试验、检验、周转等环节确定人员,严格按计划执行,上下游互相监督检查,真正做到某环节出现问题立即报告,如有要求必须随时到位,确保了各环节之间的高效衔接和并联。
打破协调范围,创新工作思路
之前产品的周转是将所有产品分解完成后统一转至机加车间,再由机加车间全部返修完成后将产品返回装配车间。由于该型号维修任务时间紧,传统的周转方式会导致资源集中、严重占用,在产品没有到现场时又会造成资源浪费。为克服这些问题,车间采用精细分解方式,将一部分产品周转至机加,返修完成一部分装配一部分,形成修理虚拟精益单元,流水作业使得资源被有效应用,全面减少了产品等待时间。
装配试验车间厂房里,有人拿着锉刀锉修,有人正在装配,有人正在试验……紧张而有条不紊的场面每天都在重复上演。在大家的通力合作下,该型号的修理时间由最早的7天,缩短到3天时间,所有项目类号及批产任务也顺利达到了既定目标。