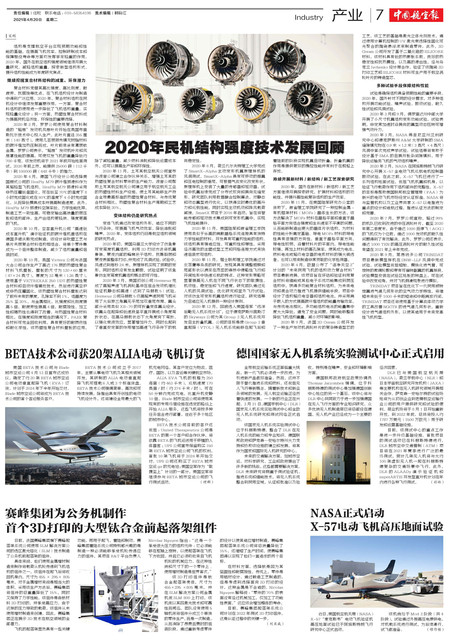
赛峰集团为公务机制作首个3D打印的大型钛合金前起落架组件

日前,法国赛峰集团旗下赛峰起落架系统公司使用SLM解决方案公司的选区激光熔化(SLM)技术制造了公务机前起落架的组件。
具体来说,他们使用金属增材制造来制作将载荷从机轮传递到飞机结构的组件之一,该组件在起飞后将收回机身内,尺寸为455 × 295× 805毫米,对于金属增材来说是相当大的体积。采用该生产方法后,赛峰集团将组件的总重量降低了15%,同时又保持了力学性能。该组件是由钛材料3D打印的,并承受高应力。由于这样的压力导致的载荷,该组件从未使用增材制造来创建。因此,赛峰集团正在展示3D技术在航空领域的全部潜力。
飞机的起落架显然具有一些关键功能,即用于起飞、着陆和制动。赛峰集团着陆系统公司特别感兴趣的是制造一种必须能够承受机轮传递应力的组件,其项目R&T平台负责人Nicolas Nguyen指出:“这是一个承受很大压力的结构元件:它必须能够在枢轴上旋转,以使起落架在飞机下方收回,并且它必须吸收来自飞机机轮的机械应力。在这种性质和尺寸下的一个零件上,使用增材制造是世界首次。”
该3D打印组件是钛合金起落架壳体,尺寸为455×295 ×805毫米,并在SLM解决方案公司金属机床SLM 800上打印,该机床以其四激光技术和可靠性而闻名。团队没有使用5轴机床将组件分成三个单独的零件生产,而是一次制造,从而消除了昂贵且费时的组装阶段。通过重新考虑零件的设计以使其适应增材制造,赛峰集团起落架系统公司将总质量降低了15%,还缩短了生产时间,使赛峰集团得以实现了他们一直追求的两个目标。
在材料方面,选择钛是因为其坚固性和耐腐蚀性。传统上,零件是用铝材设计、通过锻造工艺制造的,但是考虑到选择面向3D打印的设计,这种金属是不合适的。Nicolas Nguyen解释说:“零件的70%的表面没有经过机械加工,仅加工了功能性表面。”这应该会增加箱体的寿命。
目前,赛峰集团起落架系统公司计划在2022年测试3D打印组件,这是认证过程中的关键一步。(刘亚威)