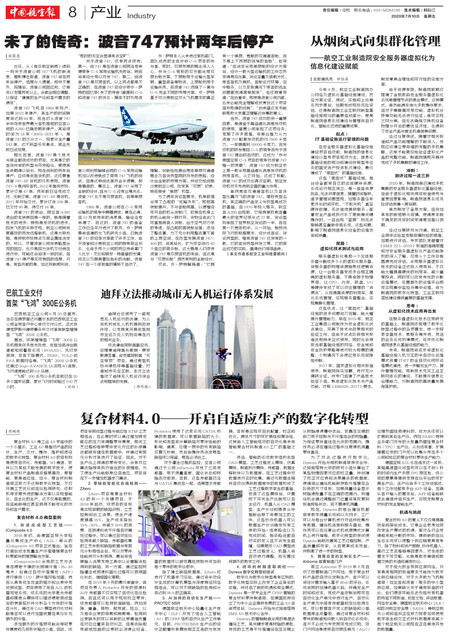
复合材料4.0——开启自适应生产的数字化转型

阴鹏艳
复合材料4.0是工业4.0宇宙中的一个小星系。工业4.0是推动产品的设计、生产、交付、操作、维护和退役的数字化转型,复合材料4.0的目标则是使用自动化、传感器、5G通信、软件以及其他不断发展的数字技术,使复合材料产品制造流程更高效、更智能、更具适应性。如今,复合材料制造商正致力于这种数字化转型,不仅开展工艺优化和在线检测研究,还积极寻求更先进的解决方案以实现智能化、自主化的生产,这不仅是敏捷的,而且能够响应甚至预测不断变化的市场和客户需求。
复合材料4.0典型案例
1.自适应成型工艺链——iComposite 4.0
2016年初,由德国亚琛大学轻量化集成生产中心(AZL)牵头的iComposite 4.0项目正式推出,旨在打造低成本批量生产纤维增强复合材料零部件的理想解决方案。
iComposite4.0采用的工艺方法是在喷射干燥的长玻璃纤维(25~30毫米)后通过自动纤维铺放(AFP)进行单向(UD)碳纤维网格加固,进而从具有成本效益的粗纱和丝束中完成预成型。项目使用了来自AZL的机器视觉系统,该系统的光学激光传感器和摄像头模块可以描述喷射预成型后的表面拓扑并分析各个方向的纤维百分比,通过与CAD模型进行比对判断是否可以进行加固或需在某处补充额外的纤维。
添加额外的纤维层可能会导致零件厚度和几何形状超过公差,因此,该项目将预成型过程与适应性RTM工艺相结合,在必要时可以通过增加特定部位的压力来调整零件厚度。相关工艺过程和每种零件变化对应的补偿算法都被存储在数据库中,并通过有限元分析对其进行了验证。因此,对于生产线上测得的零件变化,会有对应算法指导其执行适当的补偿措施。为了使生产线能够原位自适应,项目将在下一步增加机器学习算法。
2.零缺陷智能化在线检测——ZAero
ZAero项目是复合材料4.0的另一个关键项目,于2016年启动。该项目的目标是实现早期的缺陷识别、工艺控制和返工决策,使生产速度提高15%,生产成本降低15%~20%,并减少50%的浪费。在预浸料或干纤维自动铺放过程中,可以通过自动在线检测来减少缺陷。传感器收集的工艺参数和缺陷数据与有限元分析相结合后,可以对零件性能进行分析预测,最后将结果输入决策支持工具中以妥善解决检测到的缺陷。另一方面,通过监控树脂灌注或预浸料固化过程可以预测固化状态,缩短固化周期。
在2019年9月的最终审查中,由项目负责人Profactor 开发的预浸料AFP传感器不仅实现了自动化在线检测,而且还可以用于现场校正零件。该传感器可以检测标准缺陷,例如间隙、重叠、异物、起球疵、扭丝,以及每条丝束的早剪和晚剪等。检测到丝束缺失时可以将新的丝束精准放置在对应位置来自动纠正,但是去除起球疵或扭曲的丝束时必须停止设备。Profactor使用了达索系统CATIA构建的数据库,可以根据缺陷的大小、形状和类型来计算缺陷对零件性能的影响。通常,处理一层中的所有缺陷仅需几秒钟,然后由操作员决定哪些缺陷可以保留,哪些必须返工。
对于灌注过程的监控,空客公司通过子公司InFactory 开发了三类传感器,用于测量温度、固化状态和树脂流动前段。目前,这些传感器已经与CATIA集成在一起,结果显示传感器的数据可以被可靠地获取并添加到每个零件的数字线索中。
除了建立缺陷数据库,ZAero还进行了机器学习实验。通过将手动设计生成的计算机模型与深度神经网络相结合,可以对不同缺陷的检测和分类达到95%的正确率。
3. AI加持的自动化生产线——PROTEC NSR
德国航空航天中心轻量化生产技术中心(ZLP)开发了结合人工智能(AI)的CFRP结构自动化生产工作单元。目前,PROTECNSR生产线的设计正朝着所有模块相互互连的方向发展,目标是实现可自我配置、校正和优化,满足尺寸的可扩展性和复杂性。这种由人工智能驱动的自动化是未来智能复合材料制造4.0工厂的基础之一。
灵活、智能的系统数字结构包括CAD模型、工艺过程定义模块、仿真模块、制造执行模块、传感器、数据注释软件以及数据库。在工艺过程中对数据进行实时收集,通过元数据注释并自动反馈到数据库中的数据构成了
工艺过程数字孪生的基础。安装了这些模块后,只需按下开关生产线就可以自主运行。机器人从CAD模型、生产计划和摄像头中推断出接下来要加工的工件。这些协作机器人可以根据生产计划确定所有工序的开始/结束路径以及完成时间,每条路径都自动实时定义且不会发生碰撞。如果更改CAD模型或工艺过程定义,机器人将自动进行调整,而无需任何额外的教学工作。
4.闭环的树脂浸取调控——Dynexa数字化转型初尝试
数字化与数字化转型是有区别的。数字化转型实际上改变了企业背后的流程,并开启了新的机遇和商业模式。Dynexa是一家专业生产CFRP管轴的复合材料零件制造商。在德国政府设立了为中小企业提供免费的工业4.0咨询项目后,Dynexa 开始与达姆施塔特SME 4.0技术中心合作。
Dynexa的管轴制造采用的是湿法缠绕工艺,其关键步骤是树脂的浸取。传统的工艺是干纤维缠绕在压实辊上从树脂浸渍槽中滚出,紧靠压实辊的刮刀用于控制与干纤维结合的树脂量。为保证零件直径在允许的范围内,操作员必须在缠绕过程中反复停机测量零件直径。
为了对此过程进行数字化,Dynexa 开始与相机制造商寻求合作。达姆施塔特大学的研究小组计算出了某些物理因素对应的校正量,并创建了校正对应表和决策算法的数据库,使得细丝缠绕机能够获取纤维管在各阶段的尺寸目标。如果测量设备显示树脂浸取量不在正确的范围内,则缠绕机会通过调整刮刀位置将其恢复到标准规格状态,而不需停机测量。
现在,Dynexa的每台缠绕机都装有数字测量系统和以太网卡,工厂可以与每台计算机进行对话并收集所有数据。缠绕机连接到服务器后,操作员可以在任意台式机或便携式计算机上进行编程。数字化转型的尝试使Dynexa能够改善其工艺过程控制、产品质量和效率,从而更具成本效益,并刺激了进一步的转型。
5. 随需应变的定制化生产——Airborne按需制造门户
荷兰Airborne于2019年9月启动了按需制造门户网站,用于复合材料产品的自动化定制生产。客户可以将设计需求输入基于Web的平台,系统将即时创建机器代码,并确定生产时间和成本,完成产品定制后即可在自动化生产单元中进行生产。自动化生产单元中装有传感器和在线检测系统,可以根据客户定义的缺陷和公差数据库生成警报。通过将复合材料和零件的制造知识嵌入到自动化系统中,客户不必成为专家即可完成订购。该门户网站是使用自动层压单元(ALC)处理热固性预浸料的,该方法还可以扩展到其他生产线,例如SABIC特种业务部门开发的大批量热塑性复合材料(TPC)生产线。从长远来看,扩展随需应变的门户可以收集分布在多个公司和地区的复合材料零件生产能力。
德国亚琛AZL也在追求这一目标,其超高速固化成型机可以在不到5秒的时间内生产多层TPC层压板。该公司的愿景是提供支持在线平台的可扩展生产线,生产线由多个工作站组成,每个工作站都有多台AFP设备。在确认客户输入的需求后,AFP设备能够彼此通信并组织生产,实现定制复合材料的完全智能生产。
机遇与挑战
复合材料4.0的意义不仅仅是提高效率和降低成本,它是企业思考如何改变生产模式的机遇。面对各行业变得越来越分散的市场,提供新的在线生态系统可以使整个供应链更具竞争力。除了物料和资产跟踪、协作机器人、高级工艺流程链等因素外,对本体的需求不可忽略,也就是数字通信和数据交换的术语和通用协议。
对于庞大的全球供应商网络,只有具有相同的标准要求才能作为数字化供应链运作。对于大多数为飞机制造商(如空客和波音)服务的中小型供应商,如果缺乏关于通用标准的讨论,他们便很可能无法负担所有机器的两组不同标准,包括文档、评估数据、网络安全等。德国航空航天中心(DLR)和欧洲航空安全局(EASA)等航空航天公司和组织正在努力探索如何使用数字孪生和交互式材料数据库来减少每个航空航天公司现在正在单独开发的数据量。