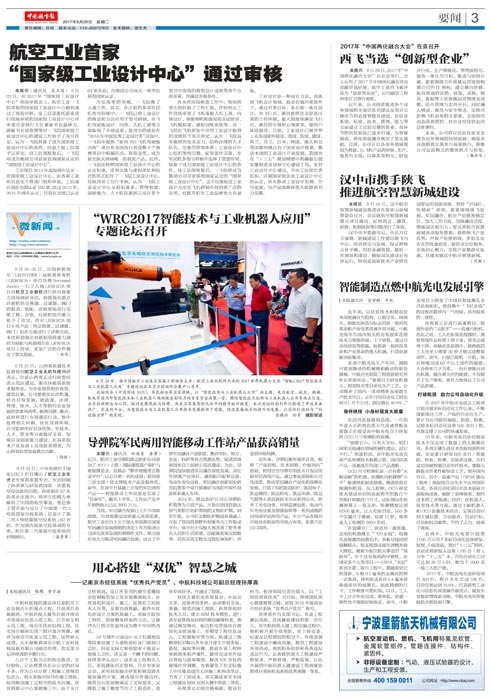
智能制造点燃中航光电发展引擎
本报通讯员 窦芳超 辛欣
近年来,以信息技术和制造技术深度融合为趋势,以数字化、网络化、智能化制造为标志的新一轮科技革命和产业变革迅速孕育兴起,中航光电作为国内领先的光电流体连接技术方案提供商,上下统筹,通过自动化研发等措施,抢抓新一轮科技革命和产业革命的重大机遇,打造创新驱动新能动。
走进中航光电生产车间,满眼可看到舞动的机械臂和跳动的银色器械。中航光电制造工程创新研究所所长张波利说:“靠着自主研发机器人、视觉技术等自动化生产工艺,公司填补了国内一项项精密连接器生产技术空白,去年月均自动化工时达到9.1万个小时,同比增长48.9% 。”
身怀绝技 小身材蕴含大能量
在民用连接器制造部,一片指甲盖大小的黑色第五代高速背板连接器正在接受由中航光电自主研发的CCD尺寸检测机的检测。
“别看它小,可有大学问。咱们国家无线通信领域的硬件建设,没它不行。”张波利说,在中航光电攻克该产品检测技术难题之前,国内同类产品一直被高价的进口产品垄断。
CCD尺寸检测机是一台有着“火眼金睛”的机器。检测机内机械臂“小手”敏捷地抓起连接器,精准地放在探测相机前。仅几秒钟,CCD视觉技术便成功识别表面密布的数百个鱼眼针和插合口尺寸,达标情况在检测屏幕上一览无余,检测精度达到0.008毫米。让人吃惊的是,500多个关键尺寸测量,仅需13秒,效率是人工检测的2000多倍。
在线簧分厂,则是另一番景象。这里的机器擅长“飞针走线”。线簧孔连接器的线簧孔中,多根导线同时接触插头,使连接器连接失效概率极大降低,被称为航空航天事业的“保险丝”。由于具有极高的可靠性,在国家多个大型项目——C919、“长征”系列火箭、探月工程中,都能看到它的身影。5根0.1毫米的金属丝按照一定规则,排布形成直径0.4毫米双曲线形状的线簧孔,如此精细的尺寸,工作难度可想而知。以往,工人手工分步作业完成,效率低,质量一致性也不能很好地保证。如今,中航光电自主研发了中国首套线簧孔全自动装配机,使得整个“飞针走线”的过程在数秒内一气呵成,具有极高的一致性。
再看看正在进行高速剪切、插接作业的“无影手”——高速凸轮机。在此之前,工人在组装连接器时,需要将部件从料带上剪下来,将毛边清理干净,再插在连接器中。最熟练的工人也至少需要30秒才能完成整套动作。如今,只要凸轮机一开机,每分钟能完成50个以上部件的插接,不合格率几乎为零。一台台智能自动化机器,蕴含着无穷的能量,不仅提升了生产效率,更有力地保证了公司产品质量。
打破瓶颈 助力公司自动化升级
自2007年中航光电成立工装项目组开展非标自动化工作以来,不断探索部分工序、产线的自动化生产,累计为公司提供装配、检验、检测、试验非标自动化设备500余台/套,有效支撑了公司的快速发展。
10年来,中航光电自动化制造技术不仅实现了数量上的大规模应用,多项关键先进技术也取得新的突破。企业累计研制500余台/套装配、检验、检测、实验类设备,先后成功突破智能自动布纤技术,掌握大路数光纤柔性板制造工艺,填补国内空白。其中,高速产品(GF3A插头/插座)装配线自动化水平达到国际先进,多项自动化项目在技术创新方面取得成效,破除了束缚效率、制约成本的工序瓶颈。同时,在机器人、视觉技术等方面,通过4轴机器人和CCD影像技术结合,实现自动识别大键位置、自动装夹、自动打标、自动卸料功能等,节约了人力,提高了效率。
近两年,中航光电累计投资1100万元用于非标自动化设备研发、复制、升级改造。预计“十三五”期间,企业还将新投入设备1100台(套),力争“十三五”末,月均自动化工时可达到28万小时,相当于1500名一线工人的产能。
2017年,中航光电在途研发项目309台,预计全年完成196台,自动化率达到15.6%。打造新型工业化与信息化深度融合新亮点,激发企业提质增效新动能,中航光电用智能制造点燃发展引擎。